Case Study: Root Cause Analysis in Warehouse Automation using Causal AI
In modern warehouse automation, identifying the root causes of package anomalies is essential for improving efficiency and minimizing errors. In this case study, we use causal analysis to trace anomalies back to their origins, offering a methodical approach to understanding failures in a simulated warehouse environment.
Advanced Root Cause Analysis Techniques in the ProfitOps Platform
Root cause analysis is a critical component of Artificial Intelligence, allowing companies to understand the underlying factors driving their performance and outcomes. The ProfitOps platform incorporates several advanced techniques for root cause analysis, leveraging the power of the graphical causal model framework. This post outlines six key techniques supported by our platform: Attribute Anomalies, Distribution Change Attribution, Feature Relevance Analysis, Mediation Analysis, Direct Arrow Strength, and Intrinsic Causal Contribution.
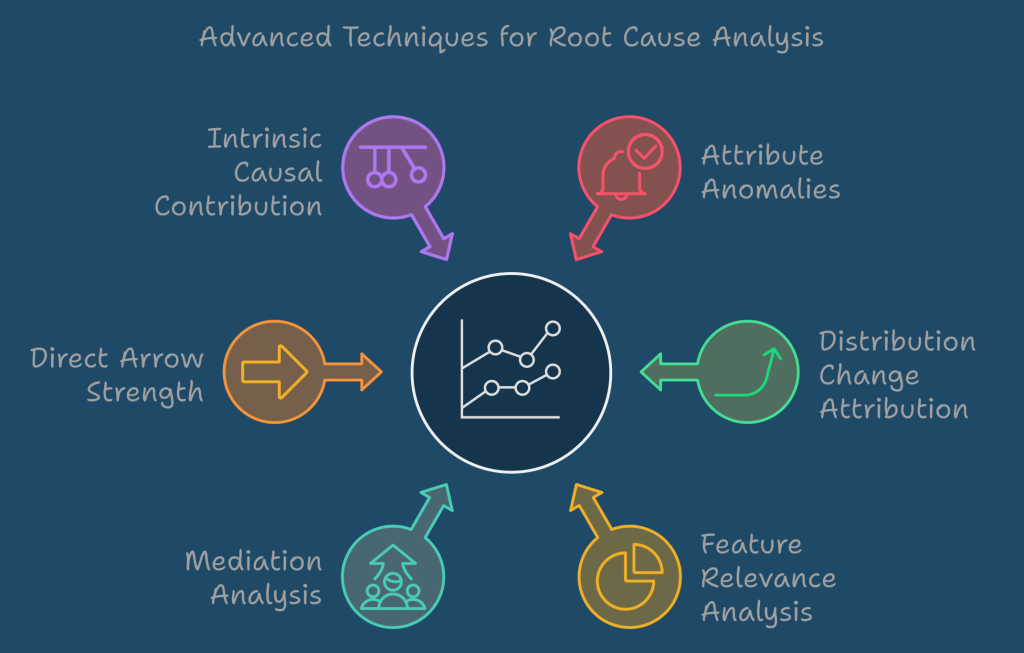
Attribute Anomalies works by asking counterfactual questions, such as “What if node X had behaved differently?”, to determine which nodes are responsible for outliers. This method systematically quantifies how much each node contributes to the anomaly. Distribution Change Attribution takes a similar approach but focuses on shifts between two data distributions, identifying which nodes in a causal graph have altered their data-generating mechanisms and explaining the corresponding changes, such as variance or divergence. Meanwhile, Feature Relevance assesses the importance of a feature by incorporating both its direct impact and the noise within the causal mechanism, offering a more comprehensive understanding of feature contribution, beyond what traditional methods like SHAP provide.
Other methods emphasize measuring causal influence within a system. Mediation Analysis breaks down the total effect of a treatment into direct and indirect pathways, highlighting how much of the effect is mediated through intermediate variables. Direct Arrow Strength quantifies the strength of a direct causal link between two nodes by measuring the effect of removing the link, offering a precise numerical value to represent this influence. Lastly, Intrinsic Causal Contribution isolates a node’s unique contribution to a system, independent of its ancestors’ effects. By analyzing how much information a node adds, using measures such as variance or entropy, this method provides a clear view of a node’s intrinsic causal role within the broader graph.
Case Study Overview
In this case study, we explore how root cause analysis can be applied to identify and rectify operational failures in an automated warehouse system, where package handling is managed through sensors and robotic processes. We simulated the processing of 1,000 packages and intentionally embedded 100 anomalies across four key areas: weight mismatches at the scale, unreadable barcodes at the scanner, sorting errors at the sorter, and diversion failures at the diverter.
By constructing a Directed Acyclic Graph (DAG) to map the relationships between the various stages of package handling, we traced the specific chains of events that led to each anomaly. This allowed us to not only detect the immediate symptoms of these issues but also uncover their root causes, such as SKU substitutions or packaging errors, which are often hidden in the complexity of the system.
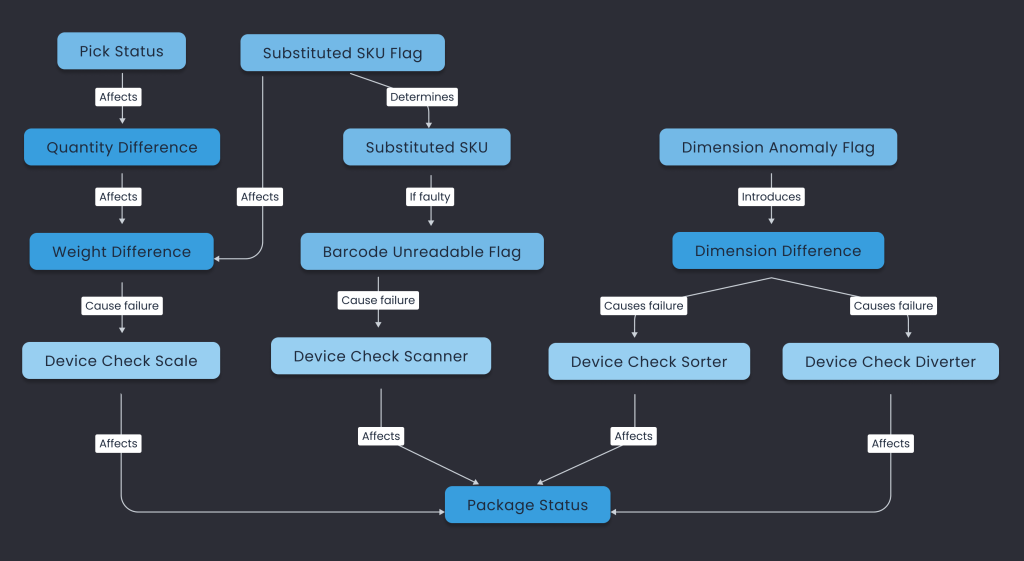
Key Anomalies and Their Root Causes
- 1. Barcode Unreadable Anomaly
In this case, a SKU with a known faulty barcode is substituted during the picking process. This triggers the Barcode Unreadable flag during the scan. The package fails the scanner check, resulting in an anomaly status.
- Root Cause: Substitution with a SKU that has a faulty barcode.
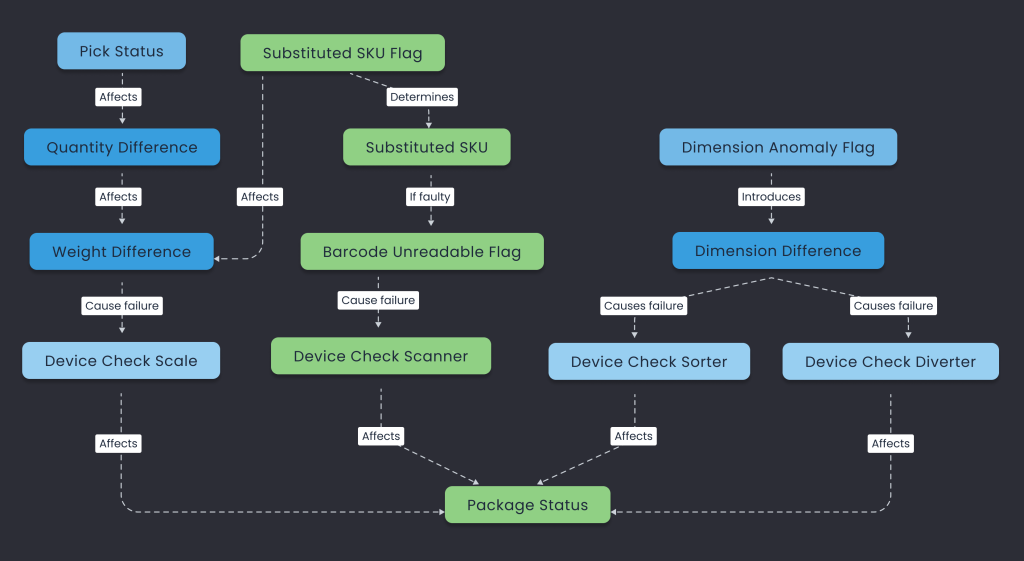
- 2. Weight Mismatch Anomaly
Here, a SKU is substituted with one of a different weight, causing a discrepancy between the actual and expected weight. When the package is checked at the scale, it fails due to this mismatch, leading to an anomaly.
- Root Cause: SKU substitution causing a weight
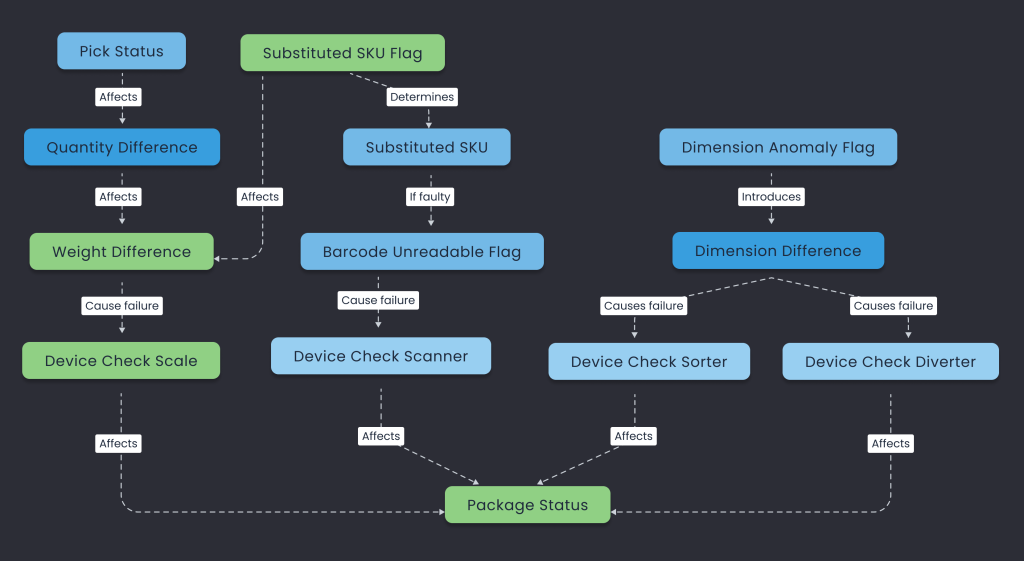
- 3. Sorting Error Anomaly
In this scenario, a dimension anomaly is introduced due to packaging errors. This results in a size difference, which prevents the sorter from correctly processing the package. The package is flagged as an anomaly.
- Root Cause: Packaging errors leading to dimension anomalies.
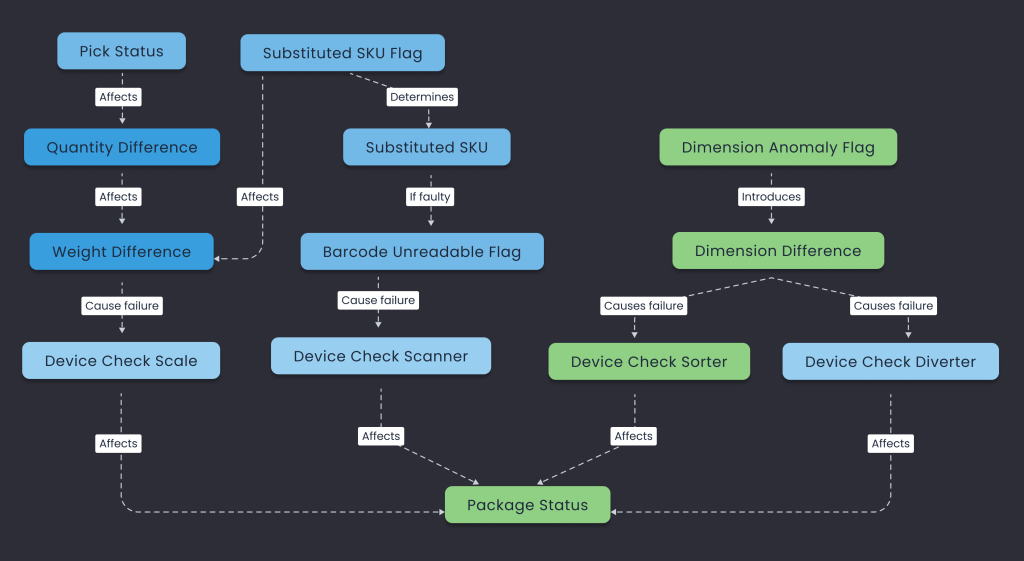
Insights and Results
By constructing a causal graph and analyzing these specific cases, we can pinpoint the exact steps that lead to package anomalies. This approach reveals not only the symptoms of failures but also their deeper causes—allowing for targeted operational improvements.
Key Takeaways:
- Causal analysis is an effective method for uncovering the origins of operational failures in complex systems.
- Data simulation with embedded anomalies provides a controlled environment to test
- Visualizing root cause paths through DAGs simplifies the understanding of complex relationships, making it easier to communicate findings and implement
By applying this methodology, warehouse managers can enhance efficiency, reduce error rates, and optimize overall performance.
Ready to transform your fulfillment strategy?
Discover how ProfitOps.ai can help you optimize your logistics, reduce costs, and streamline your order fulfillment processes. Book a demo with our experts today and see how our cutting-edge solutions can take your fulfillment operations to the next level!
Shravan Talupula
Founder, ProfitOps